Contents
Do you think all electric motors work the same way? Think again. The truth is, different motors serve different purposes—and knowing the difference can save you time, money, and effort. In this article on the Tech4Ultra Electrical website, you’ll discover the key differences between a hysteresis motor, a synchronous motor, and a single-phase motor, and learn which type is best suited for specific applications. Whether you’re a student, an engineer, or just curious about electrical machines, this guide will give you the clarity you need to choose the right motor for the job.
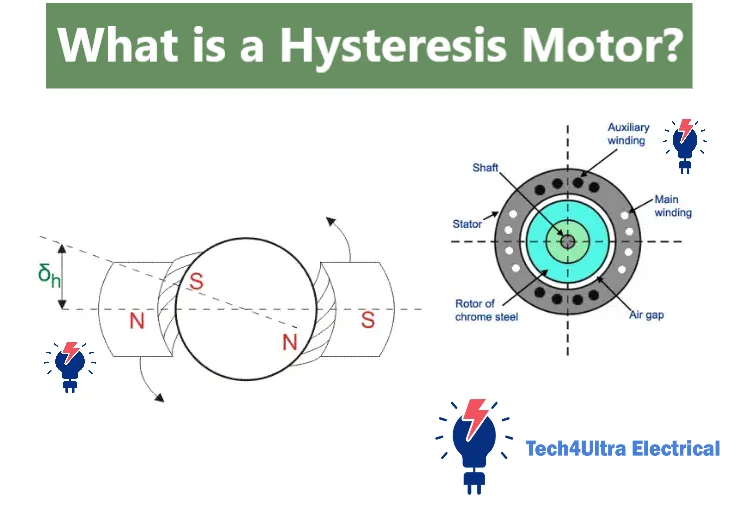
What is Hysteresis Motor?
I still remember the first time I encountered a hysteresis motor. I was troubleshooting a piece of medical equipment that had issues with smooth and quiet operation. After replacing the motor with a hysteresis type, everything changed—it ran with almost no noise, and the torque was surprisingly steady. That’s when I realized how underrated these motors really are.
A hysteresis motor is a type of synchronous motor, but it’s unique because it operates using the hysteresis loss in the rotor to produce torque. Unlike other motors, it doesn’t rely on saliency or reluctance. Instead, the rotor is made from a magnetically hard material that retains magnetism, allowing it to start like an induction motor and run synchronously without needing extra starting components.
Key Features of a Hysteresis Motor
- Provides smooth and silent operation—ideal for audio equipment, clocks, and precision tools.
- Starts without the need for additional windings or capacitors.
- Has constant speed regardless of load changes—once it reaches synchronous speed.
- Can maintain synchronization even under light loads or momentary interruptions.
Common Applications
- Electric clocks and timers
- Scientific instruments
- Audio turntables
- Medical and lab devices
Pro tip: If your application demands minimal vibration and absolute quiet, don’t overlook the hysteresis motor. It might not be as widely used as other motors, but in the right context, it’s unbeatable.
Read Also: Bipolar Stepper Motor: Working, Circuit, and Uses
Hysteresis Motor Construction and Components
When I first opened up a hysteresis motor, I expected to see something complicated. Surprisingly, it was simple—but every part had a purpose. The construction plays a major role in its quiet and stable performance, and understanding it can help you choose it for the right application.
Stator Windings
Just like in any synchronous motor, the stator of a hysteresis motor is equipped with three-phase or single-phase windings depending on the design. These windings create a rotating magnetic field that drives the rotor. What makes it different, though, is how the rotor interacts with this field.
Solid Cylindrical Rotor and Material Types
The rotor is a solid cylinder made from materials with high magnetic retentivity like cobalt alloy or chrome steel. No laminations, no windings—just a solid chunk of magnetic metal. The choice of material is crucial. Cobalt alloys, for example, offer higher torque and efficiency, but at a higher cost. Chrome steel is more affordable and still effective for most use cases.
Rotor Magnetic Memory
Here’s the genius part: the rotor’s magnetic memory. It retains part of the magnetic field even after it leaves the stator’s influence. This magnetic hysteresis is what creates the torque, especially during startup. It starts asynchronously, then locks into synchronous speed without needing extra mechanisms—just smart material physics in action.
Magnetic Hysteresis and Torque Generation
The first time I heard the term “magnetic hysteresis,” I was totally lost. It sounded like some complicated physics concept. But once I saw how it drives the torque in a hysteresis motor, it clicked—and now I can’t unsee it. It’s actually a fascinating phenomenon that gives these motors their unique performance.
What is Magnetic Hysteresis?
Magnetic hysteresis is the tendency of a magnetic material to retain some magnetization even after the external magnetic field is removed. In a hysteresis motor, this means the rotor material “remembers” the magnetism—it doesn’t instantly align or disengage with the stator’s rotating magnetic field. This memory effect is what creates a smooth torque.
Formation of Hysteresis Torque
As the stator’s magnetic field rotates, it continuously tries to magnetize the rotor in a new direction. But the rotor resists due to magnetic hysteresis. That resistance—this constant lag and re-alignment—is what generates the torque. Unlike induction motors, there’s no need for current flow in the rotor. The torque is all magnetic.
Lag Angle Explanation
The “lag angle” is the angular difference between the stator’s magnetic field and the magnetization of the rotor. It’s not constant; it changes based on load. A larger load increases the lag angle, boosting torque—up to the motor’s limit. When the load is light, the rotor locks in synchronously with minimal lag.
Role of Eddy Currents
Eddy currents also play a small supporting role. As the stator field cuts across the rotor, small currents are induced. These generate a little extra starting torque before the hysteresis torque takes over completely. They’re not the main act, but they help get things moving.
So next time you power up a single-phase motor and it runs quietly without vibration, it might just be this elegant torque mechanism doing its magic.
Working Principle: From Standstill to Synchronous Speed
Watching a hysteresis motor in action for the first time feels like seeing controlled magic. It starts quietly, picks up speed with no jolts, and then locks into perfect synchronization—no brushes, no switching, no buzzing noise. Here’s how that seamless transition actually works.
Startup Phase
At standstill, the stator windings create a rotating magnetic field. This induces eddy currents in the rotor, producing a small starting torque—enough to begin rotation. The rotor, thanks to its magnetic material, starts aligning its magnetization with the stator field. A diagram here would show how the rotor lags slightly behind the rotating stator field but gradually picks up speed.
Torque Behavior Through Synchronization
As the motor accelerates, the magnetic hysteresis effect kicks in. The rotor resists changes in magnetization due to its magnetic memory. This resistance results in a torque that remains constant across the acceleration range. Once it reaches synchronous speed, the rotor’s magnetic poles align with the stator’s rotating field, locking it into synchronized motion.
Constant Torque and Quiet Operation
The torque remains stable from low speed up to synchronization. No jerks. No variable pull. Just smooth, consistent rotation. This is one of the reasons why synchronous motors like this are favored in applications where silence and precision matter—think audio devices or lab instruments.
Unlike other single-phase motors, there’s no capacitor or centrifugal switch involved. The simplicity of design is what makes it elegant—and almost maintenance-free.
If you could see this on a chart, the torque would appear flat and steady, rising slightly due to eddy currents and then staying constant as hysteresis torque takes over until synchronization.
Torque-Speed Characteristics and Performance Curve
If you’re a visual thinker like me, the performance of a hysteresis motor really clicks once you look at its torque-speed curve. Imagine a smooth, flat line that holds steady until the motor hits synchronous speed—that’s the signature move of this motor type.
Graph Breakdown
In a typical graph (which you’d ideally plot on paper or software), the X-axis represents speed while the Y-axis shows torque. For a hysteresis motor, the curve starts with a small torque from eddy currents, rises quickly as hysteresis torque kicks in, and stays nearly flat until the motor hits synchronous speed. At that point, the rotor locks in and maintains speed with almost no slip.
Steady State Operation
What’s impressive here is how the motor holds a constant torque even under varying loads—something most single-phase motors can’t promise. Once synchronized, it resists speed changes and continues quietly and efficiently without fluctuation.
Comparison with Other Motors
- Induction motors show a sharp torque dip near synchronous speed due to slip loss.
- Reluctance motors can have irregular torque and noise at low loads.
- Hysteresis motors shine with their consistent torque and vibration-free rotation throughout the curve.
If your application values quiet stability over brute force, this motor’s curve makes a compelling case.
Types of Hysteresis Motors and Their Specific Use Cases
Not all hysteresis motors are built the same. Over time, I’ve come across different forms—some compact and flat like a pancake, others longer and cylindrical. Each type is built for a specific purpose, and knowing the difference can save you from over-engineering or under-delivering in your projects.
Cylindrical Rotor Type
This is the most common version. It features a solid, magnetically hard rotor shaped like a cylinder. It’s typically used in timing devices, tape recorders, and lab tools where smooth, consistent speed is essential. I’ve used this type in a metering pump where any jitter in motion would mess up the dosing. It performed like a champ.
Disc-Type Hysteresis Motor
The disc version is more compact and ideal for shallow mounting spaces—like in fans or record players. The rotor and stator are disc-shaped, allowing for axial magnetic fields and saving vertical space. Despite its small size, it still delivers reliable torque and speed stability.
Axial and Circumferential Field Types
Axial field types concentrate magnetic flux along the rotor’s axis—great for flat designs. Circumferential field types, on the other hand, distribute the field around the rotor, offering higher torque output in cylindrical builds. Choosing between them comes down to balancing torque needs versus form factor.
So, when selecting a synchronous motor for precision work, think beyond just speed and size—choose the design type that fits the actual task.
Advantages That Make It Unique
The first time I ran a hysteresis motor on a test bench, I had to double-check if it was actually spinning—it was that quiet. No hum. No vibration. Just smooth rotation. And that’s not an exaggeration.
No Noise, No Vibration
Because the rotor doesn’t rely on magnetic saliency or switching components, the motor runs almost silently. This makes it a go-to choice for applications where even a slight buzz is unacceptable—like in studio turntables or sensitive lab gear.
High Reliability and Smooth Operation
With no brushes, commutators, or slip rings, the hysteresis motor has fewer parts to fail. It can run for thousands of hours without maintenance. Its simple, rugged design also makes it very durable under continuous use.
Constant Torque Across Speeds
From start-up to full synchronization, the motor provides nearly flat torque. This consistent force makes it ideal for systems that need steady motion without sudden changes—something even many single-phase motors can’t handle gracefully.
Disadvantages and Limitations
As much as I admire the hysteresis motor, it’s not perfect. Like any technology, it comes with trade-offs. And if you’re thinking of using one in your next project, it’s only fair to know what you’re getting into.
Efficiency Concerns
One of the biggest drawbacks is efficiency. Because the rotor continuously resists changes in magnetization, it generates heat. This magnetic drag, while useful for torque, results in energy loss—so don’t expect stellar efficiency like you’d get from some synchronous motors.
Material Costs
The rotor materials—like cobalt alloys and chrome steel—aren’t cheap. They’re chosen for their magnetic memory, but that comes at a price. If you’re on a tight budget, especially for bulk manufacturing, this could be a dealbreaker.
Limited Torque Capacity
Compared to induction or shaded-pole motors, the hysteresis motor isn’t built for heavy lifting. It excels in light-load, precision applications. If you push it beyond its torque limit, it simply won’t sync—and that can cause unexpected stalls.
Real-World Applications
The more I worked with hysteresis motors, the more I noticed a pattern—they kept showing up in places where precision and silence weren’t optional, but essential. These aren’t your heavy-duty industrial motors, but they quietly power some of the most critical and delicate equipment out there.
High-Inertia Systems
One of the most impressive things about hysteresis motors is how well they handle high-inertia loads. Because they produce constant torque and have no cogging effect, they can bring heavy flywheels or recording platters up to speed smoothly. You’ll find them in devices where momentum matters more than speed, like centrifuges and rotating mirrors in optics labs.
Precision Equipment
Ever wonder how audio recorders keep pitch perfect, or how timers in medical devices avoid any drift? That’s where the hysteresis motor comes in. I once repaired a vintage reel-to-reel recorder, and replacing the worn-out drive motor with a hysteresis model brought it back to studio-grade accuracy—with barely a whisper of noise.
Aerospace and Laboratory Uses
In aerospace test benches and scientific labs, vibration is the enemy. These motors are ideal for driving calibration devices, analytical instruments, and any setup where mechanical disturbance must be avoided. Their predictable, synchronous behavior is trusted in critical applications.
So while they might not be flashy, hysteresis motors are often the quiet heroes behind some very high-stakes systems.
Hysteresis Motor vs Other Motor Types
When I first started working with motors, I kept asking myself, “Why choose one over another?” Once I compared the hysteresis motor side by side with more common types like induction, permanent magnet, and reluctance motors, the differences became crystal clear.
Induction Motors
Induction motors are everywhere—for good reason. They’re affordable, rugged, and efficient for general-purpose tasks. But they rely on slip to generate torque, which means fluctuating speed and noisy operation. That’s where the hysteresis motor wins—it offers constant synchronous speed and zero vibration, perfect for sensitive applications.
Permanent Magnet Motors
These motors are known for high efficiency and strong torque-to-weight ratios. However, they require complex electronics for speed control and are sensitive to load changes. In contrast, a hysteresis motor maintains steady torque without needing feedback systems—less complexity, more stability.
Reluctance Motors
Reluctance motors are cheap and efficient for basic automation, but they’re noisy and produce torque ripple. I once used one for a small pump, and the vibrations nearly ruined the bearings. Switching to a synchronous hysteresis motor solved that instantly.
In short, if your priority is precision, silence, and smooth startup—even under load—the hysteresis motor deserves a serious look.
Maintenance and Performance Tips
One of the reasons I personally love working with a hysteresis motor is how little it asks in return. Seriously—once installed properly, it runs for years with barely any attention. But if you want to extend its lifespan and keep it performing at its best, here’s what I’ve learned the hard way.
Basic Maintenance
Since there are no brushes or commutators, wear and tear is minimal. But don’t ignore the bearings—they’re usually the first to go. A light check every few months and occasional lubrication (if the bearing type allows) can make a big difference in performance.
Lifespan Considerations
A well-designed hysteresis motor can last 20,000 hours or more under continuous operation. Just avoid overloading it. These motors aren’t built for brute torque; exceeding rated load can shorten lifespan dramatically.
Noise Diagnostics
These motors are known for being whisper-quiet. If you hear humming or buzzing, it’s almost always a mechanical issue—usually bearing wear or shaft misalignment. The motor itself rarely causes noise unless it’s being pushed beyond its design limits.
Watch Also: Eddy Currents Explained: Theory, Applications, and Real-World Innovations
Future Developments and Research Trends
Even though the hysteresis motor is often seen as a legacy technology, it’s far from outdated. In fact, researchers and manufacturers are pushing its boundaries more than ever, especially as demand for quiet, high-precision motors grows in smart devices and automation systems.
Material Innovations
One of the most exciting trends is the development of advanced magnetic materials. Alloys with improved hysteresis characteristics—like rare-earth composites—are being tested to boost torque without increasing rotor size or heat losses. These materials could significantly raise efficiency while reducing the cost-to-performance ratio.
High-Efficiency Designs
New rotor geometries and hybrid stator windings are under review to reduce eddy current losses and improve power factor. The goal is to make hysteresis motors competitive with modern synchronous motors in both performance and energy ratings.
Smart Control Systems
Another big leap is integrating smart controls—sensors, digital drives, and IoT compatibility—to monitor motor health, optimize performance in real time, and automate maintenance scheduling. Imagine a single-phase motor that tells you when its bearings are wearing out before they fail.
The future is quiet, precise, and smart—and the hysteresis motor is ready to play its part.
Conclusion
By now, you’ve seen what makes the hysteresis motor stand out—its smooth, silent operation, constant torque, and minimal maintenance needs. It may not be the most powerful or the cheapest option, but when precision and reliability matter, it’s in a class of its own.
So, when should you choose a hysteresis motor? Go for it if your application demands synchronous motor behavior with no vibration—like in timing systems, audio equipment, lab devices, or compact single-phase motor setups. It’s not about brute strength; it’s about elegant, consistent performance where it counts most.
FAQs
What is the principle of hysteresis motor?
The hysteresis motor operates on the principle of magnetic hysteresis. As the stator creates a rotating magnetic field, the rotor—made from a magnetically hard material—develops magnetic poles that lag behind this field. This lag creates a torque that drives the rotor, allowing it to synchronize without external excitation or complex startup components.
What are the applications of hysteresis motor?
Hysteresis motors are used in applications requiring silent, constant-speed performance, such as electric clocks, timers, audio recorders, scientific instruments, and some aerospace or laboratory devices. They’re also common in high-inertia systems due to their ability to maintain torque without speed fluctuations.
What is the hysteresis operation?
Hysteresis operation refers to the rotor’s resistance to changes in magnetization. This characteristic allows the rotor to maintain a magnetic lag behind the stator field, producing a smooth and constant torque as the motor accelerates to synchronous speed. This mechanism ensures low noise and precise speed control.
Can a single-phase hysteresis motor run at synchronous speed?
Yes, a single-phase hysteresis motor can run at synchronous speed. It starts asynchronously using eddy current torque and then synchronizes with the stator’s rotating magnetic field thanks to the magnetic hysteresis effect. No additional circuitry is needed to achieve synchronization.
3 thoughts on “Transformer Efficiency Explained: Calculation, Losses, and Optimization Strategies”