Contents
Have you ever wondered what makes electric motors and generators perform so efficiently? The answer lies in a small but essential component called the armature. In this article on the Tech4Ultra Electrical website, you’ll discover the key role this part plays in the operation of electric motors and electric generators. We’ll break down how it works, why it’s critical, and what happens when it fails. Whether you’re into electronics or just curious about how things work, this guide will give you the insight you’ve been missing.
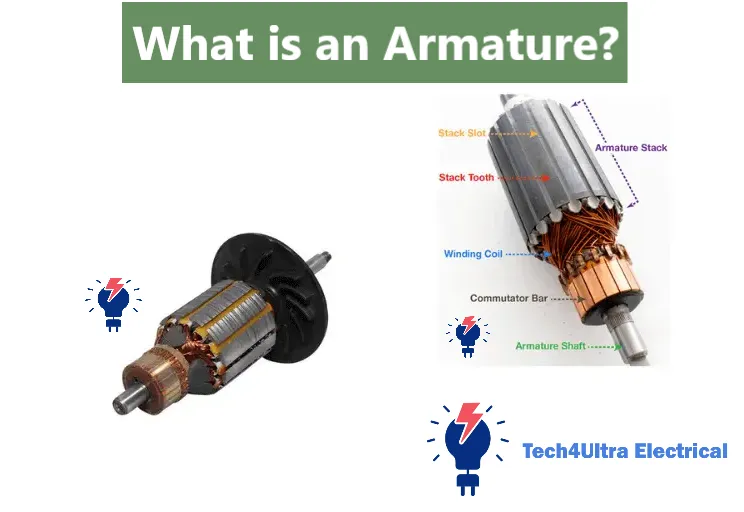
What is an armature?
I still remember the first time I opened up a broken fan to see what was inside. All those coils and parts looked confusing—until I learned about the armature. Think of it as the heart of any electric motor or electric generator. It’s a rotating component, usually made up of windings, that carries current and interacts with the magnetic field to produce motion or electricity. Without it, nothing moves, nothing powers up.
Importance in electric machines
Why does the armature matter so much? Simple—it’s where all the action happens. In a motor, it’s the part that converts electrical energy into motion. In a generator, it does the opposite: turns motion into electricity. I’ve dealt with faulty machines before, and let me tell you, a bad armature means game over. Knowing how this part works can help you diagnose issues early or even prevent damage altogether.
Read Also: Electric Generator: How It Works, Types, and Complete Guide to Electromagnetic Induction
Components of an Armature
Armature core
The first time I held a dismantled electric motor, the armature core stood out like a solid backbone—stacked laminations of steel pressed together. This part isn’t just for show. It holds the windings and reduces energy loss due to eddy currents. Without the laminated structure, motors would overheat in no time. Trust me, I’ve had my share of scorched parts before learning that detail.
Windings and coil span
Here’s where the real action begins—those neat copper windings wrapped precisely around the core. They carry the current that interacts with the magnetic field, creating torque in electric motors or inducing voltage in electric generators. I once made the mistake of rewinding a coil too tightly and ended up with short circuits. Coil span, or the distance between the slots the wire occupies, matters more than you’d expect. Too small, and the performance suffers. Too wide, and you risk inefficient operation.
Commutator
If you’ve seen a ring of copper segments at the end of the armature, that’s the commutator. It’s the part that flips the current direction in DC motors, ensuring continuous rotation. I remember replacing one that was worn out, and the improvement was immediate—no more erratic spinning or sparking. Keeping it clean and smooth is crucial for performance.
Shaft and brushes
Lastly, the shaft runs through the center of the armature, holding everything together and transferring motion. The brushes ride on the commutator, delivering current to the windings. I’ve had brushes wear out silently, causing a drop in power that puzzled me for hours. Lesson learned: always check brush condition during maintenance.
Types of Armature
DC vs AC applications
Early in my repair journey, I didn’t realize that armatures aren’t exactly universal. DC and AC machines use them differently. In DC motors and electric generators, the armature is where both current is carried and magnetic interaction happens. It works with a commutator to handle current direction. But in AC machines, especially synchronous ones, the armature often just handles voltage generation or reception, and there’s no commutator involved.
One time, I tried swapping a part from an AC fan into a DC setup. Big mistake—nothing worked right. Understanding these differences saved me from repeating that headache again.
Gramme ring vs drum type armature
I first saw a Gramme ring in an old generator from the 1920s—it looked like something out of a museum. The coil winds around a ring, but most of the wire doesn’t cut through the magnetic field efficiently. The newer design, the drum type, is what you’ll find in nearly every modern electric motor today. It’s more compact, more efficient, and delivers better torque.
So if you’re troubleshooting or designing, always know which type you’re dealing with—form matters as much as function.
Armature in Electric Motor
Role in converting electrical to mechanical energy
The first time I got a small electric motor to spin on my workbench, I couldn’t stop smiling. That hum, that smooth rotation—it all comes down to the armature. It’s the key player in converting electrical energy into motion. When current flows through its windings, it interacts with the magnetic field and generates torque. It’s like magic, but rooted in physics.
Miss a wire, or connect it wrong, and you get sparks—or nothing. That’s how I learned to respect this part. No armature, no motion. Just dead silence and frustration.
Interaction with stator and rotor
Understanding how the armature works with the stator and rotor took me a while. In most DC motors, the armature itself is the rotating part—the rotor—while the stator stays still and provides a magnetic field. The brushes feed current into the armature via the commutator, and the resulting magnetic interaction is what drives rotation.
I used to think the stator did all the work. But once I replaced a faulty armature, the difference was night and day. Smooth operation, better power—everything just clicked. When the stator and armature are in sync, your motor runs like it’s brand new.
Armature in Electric Generator
How it generates electromotive force (EMF)
The first time I cranked a hand-powered electric generator and saw a bulb light up, I was amazed. That little glow? All thanks to the armature. In a generator, the armature’s job is to cut through magnetic field lines, and this motion induces voltage—what we call electromotive force (EMF). The faster the armature rotates, the stronger the EMF.
Back in school, it sounded abstract. But when I saw it in action—spinning the rotor and watching volts register on a meter—it made total sense. The armature turns mechanical energy into something usable. That’s power in the truest sense.
Magnetic field interaction
Here’s the thing—no magnetic field, no voltage. The armature depends on the presence of a magnetic field, either from permanent magnets or field windings. As the armature spins, each coil loop slices through the field, inducing current. I once had a generator that produced nothing, and after hours of testing, I found the field coil wasn’t getting power—so no magnetic field, no interaction.
That lesson stuck. If you ever troubleshoot a dead generator, always check the magnetic source first. Without that interaction, the armature is just spinning metal doing nothing.
Armature Reaction Explained
What it is and how it occurs
The first time I heard the term “armature reaction,” I brushed it off as just another textbook term. But then I faced a weird issue—my electric generator was producing unstable voltage, and motors were running hotter than usual. Turns out, armature reaction was the culprit. It happens when the magnetic field created by the current in the armature windings starts to interfere with the main magnetic field of the machine.
Basically, the armature isn’t just a passive player. When it’s carrying current, it generates its own magnetic field, and that can distort or weaken the original field from the stator or field windings. This shift in the field lines causes brush sparking in DC machines and lowers efficiency. I had no idea something so invisible could mess things up that badly.
Effects and solutions (interpole, compensating winding)
So how do you fix it? After digging around and asking a few pros, I learned about two key solutions: **interpoles** and **compensating windings**. Interpoles are small poles placed between the main poles to counteract the distortion. I installed a set in a DC motor once—it was like night and day. Sparking? Gone. Performance? Smooth as butter.
Compensating windings, on the other hand, are embedded into the pole faces and carry current in a direction that cancels out the armature‘s field. They’re a bit more complex to wire, but they work wonders in heavy-duty applications. If you’re building or repairing motors for continuous use, these aren’t optional—they’re essential.
Difference Between Armature and Rotor
Clear table format comparison
I used to think the armature and rotor were always the same thing—until I worked on an AC alternator. That’s when it clicked: they’re not always identical. Sometimes the armature is the rotating part (the rotor), and other times, it’s the stationary part (the stator). Here’s a simple comparison table that cleared up the confusion for me:
Feature | Armature | Rotor |
---|---|---|
Function | Handles power exchange (voltage/current) | Rotates to create mechanical interaction |
Position | Can be rotating or stationary | Always rotates |
Application (DC Motor) | Acts as the rotor | Same as armature |
Application (AC Generator) | Acts as the stator | Contains field windings |
Examples from real machines
In a typical car alternator, the armature is stationary and built into the housing, while the rotor spins inside with the field winding. But in a basic DC motor, the armature is the rotating part—you can actually see the commutator and brushes interacting with it. Knowing this saved me from ordering the wrong part once. Lesson learned: always check the setup before you assume anything.
Armature Testing and Maintenance
Growler test
The first time I saw a growler test in action, I thought it was some kind of science experiment. Turns out, it’s one of the best tools for testing a armature. The growler is a simple device that uses magnetic induction to detect shorts in the windings. You place the armature on the growler, turn it on, and sweep a hacksaw blade or metal strip over the slots. If the blade vibrates or “growls,” there’s a short circuit.
It’s old-school, but incredibly reliable. I’ve diagnosed dozens of faulty electric motors this way—fast and spot-on.
Signs of faults
Some issues are easy to spot. Burn marks, uneven wear on the commutator, and a burnt smell are dead giveaways. If your motor runs hot, has weak torque, or shoots sparks, the armature might be to blame. I once ignored minor sparking, thinking it was normal—until the motor died completely.
Common repairs
Repairs usually involve rewinding the coil, turning or cleaning the commutator, or replacing the brushes. Rewinding can be tedious—I’ve done it by hand—but it’s worth it if you want to save a solid motor. Just make sure to insulate properly and match the winding pattern.
Watch Also: Motor Protection Guide: Types, Devices, Faults & NEC Selection Tips
Applications of Armatures in Industry
Electric vehicles, power tools, generators
From the cordless drill in my garage to the electric bus I ride to work—armatures are everywhere. In electric vehicles, they sit at the core of traction motors, converting battery power into motion. I’ve seen how high-performance EV motors depend on precise armature design to deliver torque instantly.
Power tools like grinders and drills also rely on small, high-speed electric motors with efficient armatures. I once rebuilt a damaged one in my angle grinder and felt the difference right away—more control, less overheating. And of course, in electric generators, armatures are key to converting motion into power, whether it’s wind turbines or diesel gensets.
Innovations in armature technology
The game is changing fast. We’re seeing the rise of lightweight materials, better insulation coatings, and precision manufacturing. Some new designs even use carbon fiber composites to reduce weight while increasing strength. These innovations are pushing efficiency up and wear down—especially in demanding industries like aerospace and robotics.
Conclusion
By now, you’ve probably realized just how central the armature is in the world of electric motors and electric generators. Whether it’s powering a tool, lighting up a home, or driving an electric car, this humble component does the heavy lifting—quietly and consistently. I used to overlook it myself until I started tearing down machines and seeing how often the issue traced back to this one part.
If you’re diving into repairs, design, or just curious about how things work, learning about the armature is a solid place to start. It’s not flashy, but it’s essential. Keep it maintained, know how to spot issues, and you’ll save time, money, and frustration down the road.
Got a question about a motor or generator you’re working on? Drop it in the comments or check out our other guides—there’s always more to learn.
FAQs
What is the function of the armature in an electric generator?
In an electric generator, the armature is responsible for generating electricity. As it rotates within a magnetic field, it cuts through magnetic lines of force, which induces voltage in the windings. This voltage is then used to power electrical loads.
What is the function of the armature in a motor?
In an electric motor, the armature receives electrical current and converts it into mechanical motion through interaction with the magnetic field. It’s the part that actually spins to drive gears, shafts, or wheels depending on the machine.
What is the definition of armature?
An armature is the part of an electric machine—motor or generator—that carries current and interacts with a magnetic field to either produce or use motion. It typically includes the core, windings, commutator, and shaft.
What are the four parts of an armature?
The four main parts of an armature are:
- Armature core – laminated steel that supports the windings.
- Windings – copper coils where current flows.
- Commutator – a segmented ring that directs current flow (used in DC machines).
- Shaft – the central rod that transfers mechanical energy.
What are the four basic parts of a motor?
The four basic parts of a typical electric motor are:
- Armature – The rotating part that carries current and generates torque.
- Stator – The stationary part that provides a magnetic field.
- Commutator – Found in DC motors, it switches the direction of current in the armature.
- Brushes – They conduct current between stationary wires and the rotating commutator.
What is the difference between stator and armature?
The stator is the stationary part of a machine that usually provides the magnetic field, while the armature is the part that carries current and interacts with that field. In AC machines, the armature is often the stator. In DC machines, the armature is usually the rotor. Their roles depend on the machine type, but they always work together to create or use motion and electricity.
1 thought on “EMF Equation of Transformer Explained: Turns, Voltage, and Formula”